What is Hydraulic Power Pack ?
A hydraulic power pack is a device that can generate and store hydraulic energy for use in hydraulic systems. This energy can then be utilized by those systems. A pump, a motor, a reservoir, and a control valve are the typical components that make up this system.
Are You Looking for top hydraulic power pack manufacturers then get in touch with Canara hydraulics
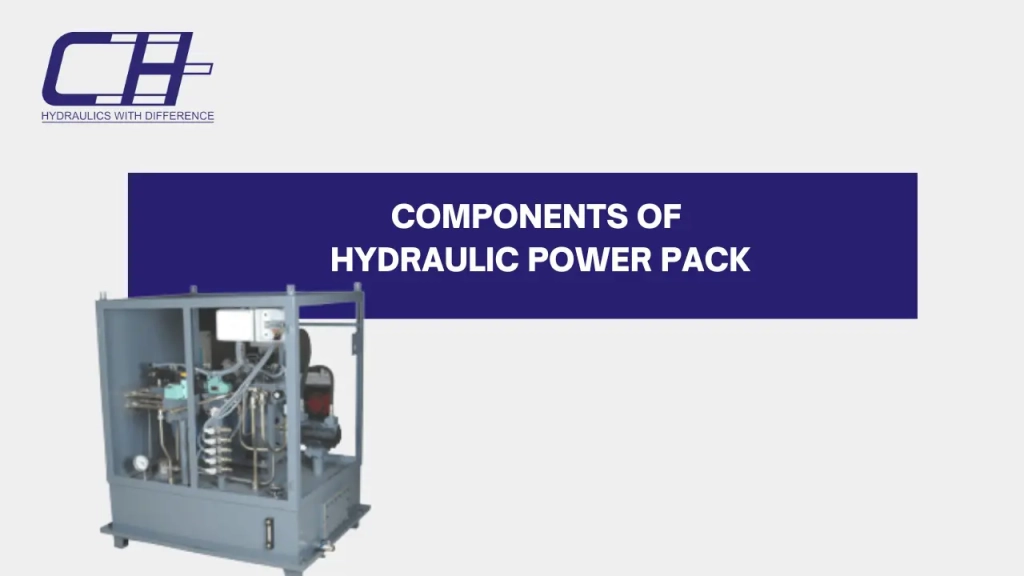
Hydraulic actuators, such as cylinders or motors, are powered by pressurized hydraulic fluid, which is first kept in the reservoir after being compressed by the pump and then directed through the control valve to power the hydraulic actuators. This makes for an easy and effective method of conveying power and motion in a broad variety of applications, such as mobile vehicles, industrial machinery, and construction equipment, amongst others.
Components Of Hydraulic Power Pack
A hydraulic power pack typically includes the following components:
Electric motor
An electric motor is the component of a hydraulic power pack that is responsible for operating the pump. This pressurises the hydraulic fluid, which in turn creates the power that is necessary for the hydraulic equipment to function.
It is possible for the electric motor to be either AC or DC, depending on the particular design of the power pack and the requirements of the application. In most cases, a motor with a high torque is used since it is capable of delivering the necessary amount of power output to keep the hydraulic system operating well.
The operator is able to make any necessary adjustments to the amount of hydraulic power that is being produced as a result of the motor’s speed and power being controlled by a drive or control system.
Gear Pump
In hydraulic power packs, the positive displacement pump known as a gear pump is typically employed because of its gear-driven design.
It does its job by entrapping fluid and moving it from one port to another using two gears that rotate in opposite directions. As a result of the gears meshing together, pockets of fluid are created, which are then transported from the input to the outlet.
Because of the rotation of the gears, the fluid is entrapped and forced to pass through the pump, which results in the creation of pressure that can be utilised to control hydraulic machinery. Because they are straightforward, dependable, and able to withstand significant pressure, gear pumps are frequently utilised in hydraulic power packs.
They are also able to handle a wide variety of fluids, including liquids of high viscosity, which makes them useful for a number of hydraulic applications. This versatility makes them ideal for use in hydraulic systems.
Reservoir tank
The hydraulic fluid is kept in a hydraulic power pack’s reservoir tank, which also acts as a storage place for the fluid. Because it offers a space in which the fluid can expand and contract in response to the pump’s ability to pressurise and depressurize it, it is a crucial component of the hydraulic system.
The reservoir provides a vast surface area for heat to dissipate, which helps to extend the life of the hydraulic components. In addition, the reservoir helps to cool the fluid, which also serves to extend the life of the hydraulic components.
A filter, a breather cap, and a drain valve are typically installed in the tank so that it may be easily maintained. The tank is typically composed of either metal or plastic. Monitoring the level of fluid in the reservoir on a frequent basis is required in order to both guarantee that there is sufficient fluid for the hydraulic system to function properly and prevent air from entering the system, which can lead to cavitation and lead to the pump being damaged.
Control Valve
In a hydraulic power pack, a control valve is a valve that is used to regulate the flow of hydraulic fluid and control the speed, direction, and pressure of the hydraulic system.
This valve may also be referred to as a directional control valve. Because it gives the operator the ability to manage how the hydraulic equipment works, it is a crucial part of the system that controls the hydraulics. Control valves can be operated manually or automatically, and they are available in a wide variety of forms, including check valves, pressure control valves, flow control valves, and directional control valves, among others.
To control the flow of fluid to a single hydraulic cylinder, several hydraulic cylinders, or a hydraulic motor, the control valve can be utilised in a variety of different ways, depending on the specific application. In order to guarantee the smooth and risk-free operation of the hydraulic system, it is essential to select the appropriate kind of control valve for the task at hand.
Relief valve
When installed in a hydraulic power pack, a relief valve functions as a safety valve to prevent the hydraulic system and equipment from being damaged by being subjected to an excessive amount of pressure.
When the pressure in the system reaches a predetermined threshold, it is programmed to open and let out any excess pressure that has built up. This protects the hydraulic components from damage and keeps both the user and the piece of equipment from being put in danger.
Typically, the relief valve is connected to the reservoir tank and is situated in the circuit close to where the control valve is located. The pressure at which the valve will open can be adjusted by the operator thanks to the fact that it is adjustable.
If the pressure in the system is higher than the limit that has been set, the valve will open. This will allow any extra fluid to flow back into the reservoir, which will result in the pressure in the system being lowered. In hydraulic systems, relief valves serve as an essential component of the safety infrastructure, and compliance with safety rules necessitates their use in a variety of applications.
Filter
Hydraulic power packs typically include filters that are responsible for removing impurities from the hydraulic fluid.
Because it serves to extend the life of the other components in the system and improves the system’s overall performance, it is a key component in the hydraulic system. The filter is typically situated in the return line, which comes into play after the fluid has been put to use in some capacity.
Before the fluid is put back into the reservoir, this process filters out any debris, moisture, and other impurities that may be present in it. This helps to maintain the cleanliness of the fluid and lowers the wear and tear on the various components.
Filters can be constructed of paper, mesh, or any number of other materials, and they can have either a single stage or numerous stages, depending on the application in question and the desired degree of filtration. To maintain the effectiveness and dependability of the hydraulic system, it is required to perform routine maintenance and to change out the filter element on a consistent basis.
Pressure Guage
A hydraulic power pack will have a device called a pressure gauge that is used to measure the pressure of the hydraulic fluid that is contained within the system.
It displays the pressure in either pounds per square inch (psi) or bars and is often positioned on the control panel or in close proximity to the reservoir. When it comes to monitoring the performance of the hydraulic system and making certain that the components are functioning within the appropriate pressure range, the pressure gauge is an essential piece of equipment to have.
The pressure gauge offers real-time information on the pressure within the system, which enables the operator to make adjustments to the control valve as required to ensure that the system continues to function at its highest possible level. By indicating changes in the pressure measurements, it also helps to detect any possible problems that may exist within the system, such as a filter that is clogged or a pump that has been broken.
It is essential to do routine checks on the pressure gauge in order to ensure that the hydraulic power pack is operating in an effective and risk-free manner.
Suction Strainer
A suction strainer is a device that is used in a hydraulic power pack to filter impurities from the hydraulic fluid before it enters the pump. This device is called a suction strainer. It helps to protect the pump from harm that could be caused by particles, debris, and other impurities that might be present in the fluid.
It is normally situated close to the entrance of the pump. The suction strainer is often a cylinder-shaped device that has a mesh or perforated metal screen. This screen is designed to let the fluid travel past it while also capturing any pollutants that may be present. The strainer helps to guarantee that the fluid that is being pumped into the pump is clean and free of debris.
This not only serves to improve the overall efficiency of the hydraulic system but also helps to extend the life of the pump. It is essential to perform routine maintenance and cleaning on the suction strainer in order to guarantee that it is operating correctly and to protect the pump and any other hydraulic components from being harmed.
Check valve
When installed in a hydraulic power pack, a check valve serves the purpose of preventing fluid from flowing in the opposite direction.
This helps to maintain the intended direction of fluid flow within the system, which in turn helps to preserve the system’s integrity and prevents damage to its components.
In most cases, the check valve will operate on its own and will not require any additional power or control from the outside.
Accumulator (optional)
In a hydraulic power pack system, an accumulator is a component that can be added if desired. It functions as a short-term energy storage device that helps to maintain a constant pressure within the system, reduces the effects of shock and surge loads, and enhances the effectiveness of the system.
The accumulator is a storage device for hydraulic fluid that is pressurised, and it is responsible for releasing the fluid at the appropriate time in order to maintain the pressure of the system during times of high demand.
This helps to reduce the load that the pump is under, which in turn helps to prevent the system from failing due to pressure drops. There are several distinct kinds of accumulators, such as bladder, piston, and diaphragm accumulators; each of these accumulators has its own set of benefits and drawbacks.